项目描述
1. 某焊接油罐项目,采用KAKUc4机器人MAG(气保焊)摆焊的焊接方式,焊接类型主要是油罐体内内角焊接,焊接工件材料304不锈钢。
2.工作站采用,多工位焊接工作形式,由工人带内圈焊接点,固定内圈位置,再用行吊吊焊接工位,由传感器扫描内圈与油罐内壁交错位置和焊接面特征识别出机器人焊接位置与焊接姿态。
3.在原来的生产流程是靠人工来固定内圈,固定,固定完之后吊到焊接工位上,通过人工重新示教焊接点位,生产时间也很长,因内圈每次位置不固定,导致每一次来件都需要人工重新修点,导致产能有限,速度较慢。
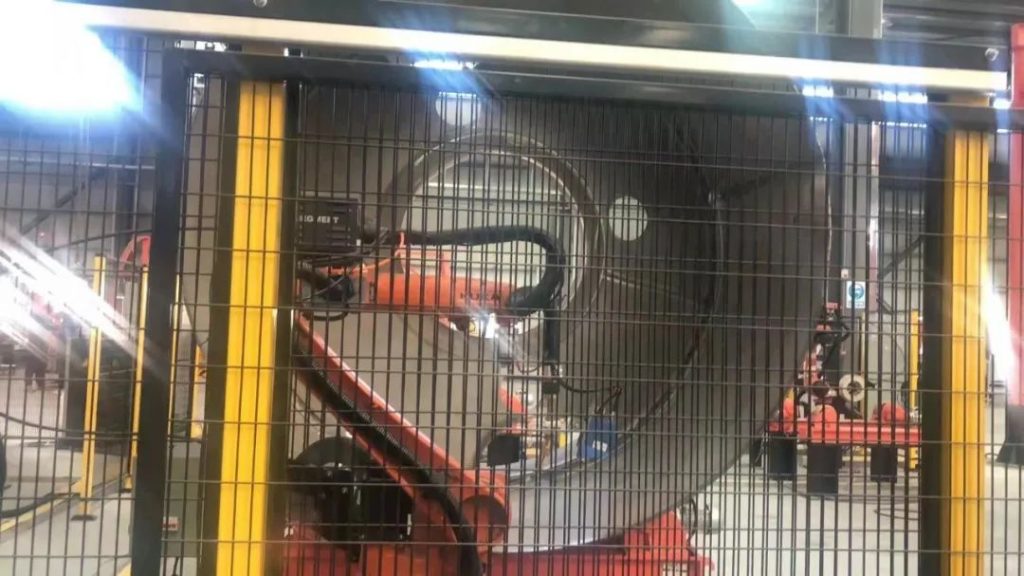
图.整体工作站
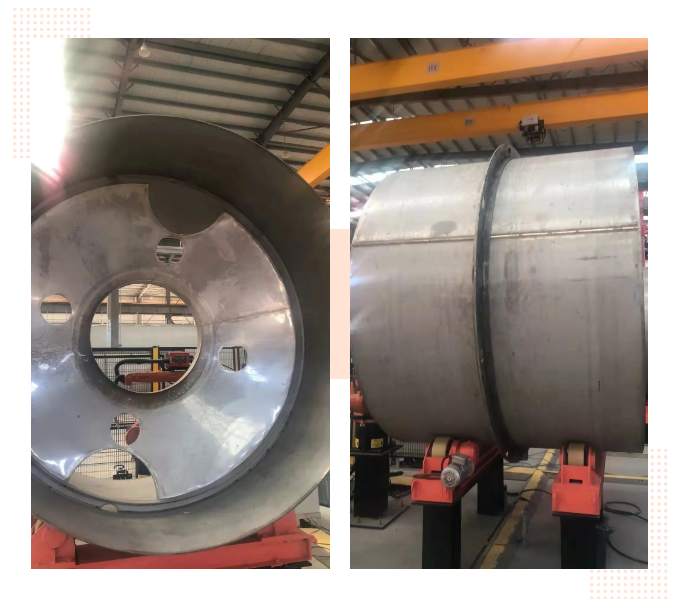
图.油罐工件
项目难点分析
1.由于焊接作业时会涉及到外部轴移动,通外部电机就行旋转过,会面临重复定位误差的问题,会影响我们传感器的扫描起点跟终点的判断、运动轨迹算法的问题,这是一个很大的挑战。
2. 现在工作站在没有传感器扫描的情况下,无法正常焊接,由于内圈与油罐位置不确定,之前的程序焊接点无法继续使用,导致传统的示教焊接无法正常焊接。
3.因此,客户希望添加我们传感器跟踪设备来替代传统的示教焊接,来减少人工维护时间和提高成品效率。焊接工件的油罐特殊性,内圈、外形多变化,每一条内圈固定位置都不一样,把内圈与油罐拼装在一起时,位置的不确定性,最高可达到10cm—100cm位置差,对于传感器的检测范围和识别精度有一定的要求。
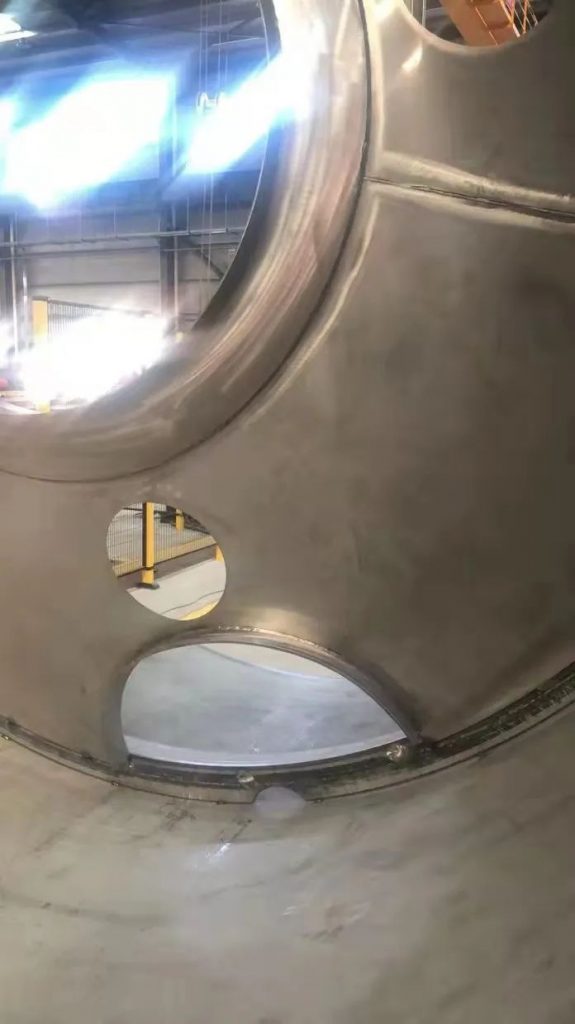
图.工件焊缝细节
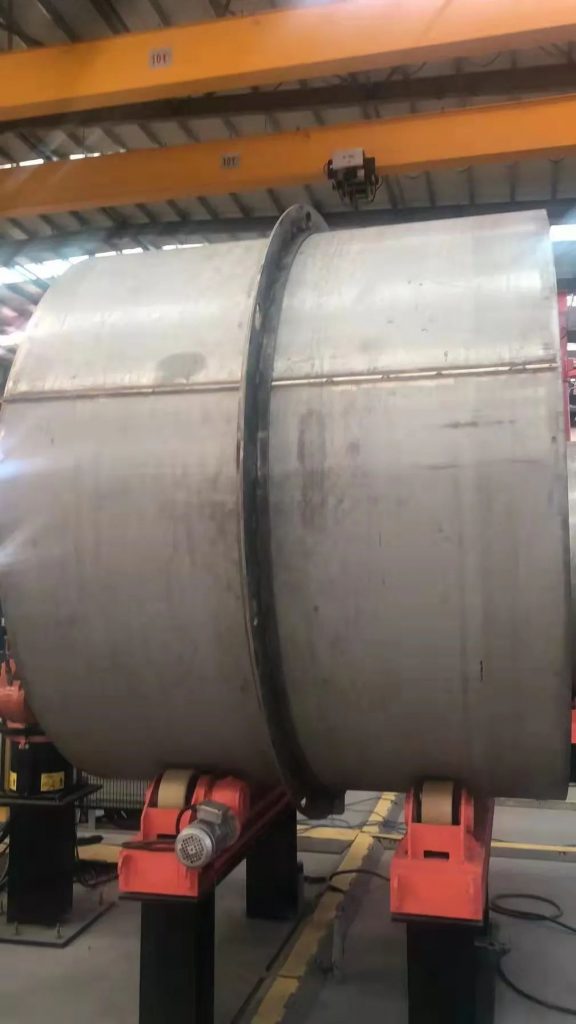
图.焊接工件实物
应用亮点
1. 无联动外部轴实现了定点摆动跟踪。
2. 焊点、异常区域轨迹过滤功能,机器人焊接过程更加稳定。
3.起始点搜索和结束点判断。通过寻位搜索焊接起始点,通过实时检测判断焊接终点,从而起始和结束位置准确接合。
4.实现敏越科技大型环焊缝焊接数字孪生技术。